Any facility that uses processed fluids or heavy-duty machinery that generates heat needs an industrial chiller system to control their processes and internal machine components.
Many different types of chillers are available for these actions, and among the best of them is the water chiller. However, what is a chiller? What is a water chiller? How does water chiller work?
In this article, we hope to provide you with all the necessary information about chillers, and water chillers, in particular, that might benefit your business.
What is a chiller?
A chiller is basically a refrigeration system that is used to lower the temperature of certain machinery, industrial spaces, and process fluids by removing heat from the system and transferring it in another place.
They are crucial for temperature regulation in several industrial processes such as injection molding, metal plating, oilfield production, food processing, and they work on three principles:
1. Phase Change
A liquid coolant undergoes a phase change into a gas when heated, and when the gaseous coolant is supercooled, it condenses back into a liquid.
2. Heat Flow
Heat energy flows from an area of high concentration to an area of low concentration.
3. Boiling Point
If the pressure is reduced over a liquid, it decreases its boiling point and vice versa.
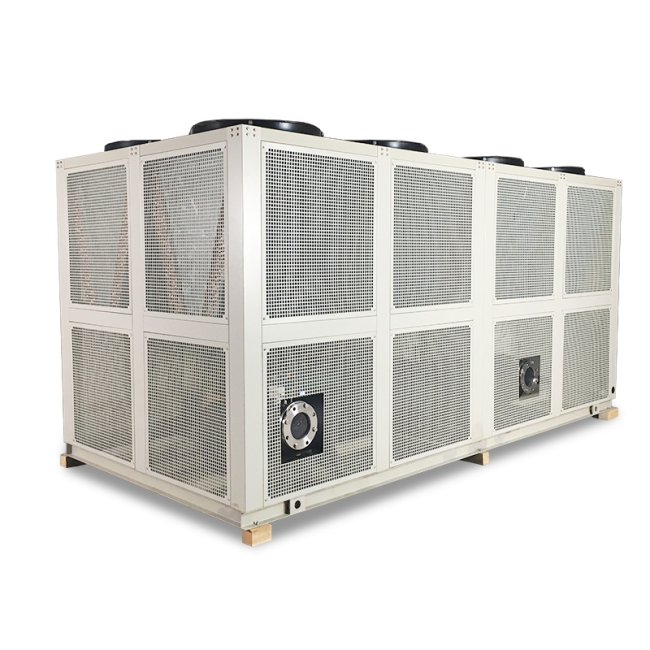
How does chiller work?
The chiller consists of four basic components:
– The compressor
– The condenser
– The expansion unit
– The evaporator
Every type of chiller system also contains a refrigerant. The process starts with a low-pressure refrigerant entering the evaporator. Inside the evaporator, the refrigerant is heated, and this causes it to undergo a phase change into a gas.
The gaseous refrigerant goes into the compressor which increases its pressure. The high-pressure refrigerant goes to the condenser which rejects the heat using cooling water from a cooling tower or air, condensing it into a high-pressure liquid.
The condensed refrigerant then goes to the expansion unit which has a valve that acts as a metering device to limit the flow of refrigerant in the system. At the same time, this lowers the pressure of the refrigerant and begins the cooling process once again.
This process is called the refrigeration cycle. In our modern world, there are currently three types of industrial chillers, the air-cooled chillers, water-cooled chillers, and absorption chillers.
Cooling towers
These huge structures are basically large heat exchanging units that provide cooling water to remove heat from a coolant that has been used to cool machinery, process fluids, or buildings.
When the cooling water meets with air, a small portion evaporates, lowering its temperature. This process is known as evaporative cooling.
It is quite common for cooling towers to be placed near bodies of water such as lakes or rivers to ensure a constant supply of water for cooling. Often, chillers and cooling towers are paired together for more efficient industrial chilling.