What is a water chiller?
Industrial chillers are used for a variety of applications where water or liquids are circulated through processing equipment for cooling. Chillers are typically used to cool products and machinery and can be used in a number of different applications including injection moulding, tooling and die-cutting, food and beverage, chemicals, lasers, machine tools, semiconductors and many more.
The function of an industrial chiller is to transfer heat from one location (usually the processing equipment or product) to another location (usually the air outside the manufacturing plant). Heat is usually transferred to or from the chiller using water or a water/glycol solution, which may require the process chiller to have a reservoir and pumping system. Whatever your industry and process, ensuring there is sufficient cooling is essential to increase productivity and save costs.
Why use a water chiller?
No industrial process, machine or motor can run 100% efficiently and heat is the most common by-product of these inefficiencies. If this heat is not eliminated, it will build up over time, reducing production times, shutting down equipment or even causing premature failure. It is necessary to incorporate cooling technology into the design of industrial process systems to avoid these problems.
There are many benefits to using chillers to provide cooling. Chillers provide consistent temperatures and pressures for your industrial processes. Eliminating temperature and pressure variables simplifies the process development and optimisation process, thus ensuring the highest quality product. In place of wasteful single-pass systems, chillers recirculate cooling water. Recirculation minimises the cost of water consumption, which can be expensive and detrimental to the environment.
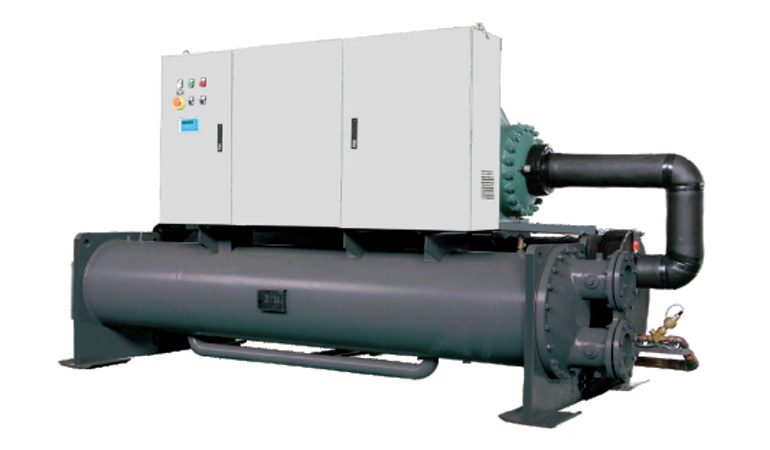
How do chillers work?
In most process cooling applications, a pump system circulates chilled water or a water/glycol solution from the chiller to the process. This cold fluid removes heat from the process, while the hot fluid is returned to the chiller. Process water is how the heat is transferred from the process to the cooler.
Process coolers contain a chemical compound called a refrigerant. There are various types of refrigerant and their application depends on the temperature required, but they are all based on the basic principle of compression and phase change as the refrigerant changes from a liquid to a gas and then back to a liquid again. The process of heating and cooling the refrigerant and changing it from a gas to a liquid and back again is the refrigeration cycle.
The refrigeration cycle starts with a low pressure liquid/gas mixture entering the evaporator. In the evaporator, the heat from the process water or water/glycol solution causes the refrigerant to boil, which changes it from a low-pressure liquid to a low-pressure gas. The low pressure gas enters the compressor where it is compressed into a high pressure gas. The high pressure gas enters the condenser where the surrounding air or condensate removes the heat and cools it to a high-pressure liquid. The high pressure liquid flows to an expansion valve which controls how much liquid refrigerant enters the evaporator, thus starting the refrigeration cycle again.
Two types of the condenser are used in water chillers. Air-cooled and water-cooled. An air-cooled condenser uses ambient air to cool the hot refrigerant gas and condense it back into the liquid state. It can be located inside or outside the chiller, but ultimately it radiates heat from the chiller into the air. In a water-cooled condenser, water from a cooling tower cools and condenses the refrigerant.
Which cooler is best for your process?
Chillers are available in a wide range of sizes and designs, from small, localised or portable chillers for small applications to large central chillers designed to provide cooling for the entire process.
If you are interested in more detailed information on the best cooling solution for your application, please contact us.